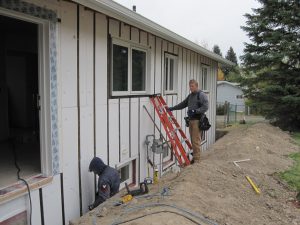
Exterior 2.5-inch high-density polystyrene installed flush to 3.5-inch exterior window jamb extension.
I’ve done three superinsulation retrofits. The cost range is somewhere in the range of $35 to $70 per square foot of conditioned floor space.
The best opportunity for a superinsulation retrofit is when you’re remodeling or renovating a home.
Costs and Benefits of Superinsulation
My most successful superinsulation retrofit, which is my current home, uses less than 20% of what ASHRAE calls an energy-efficient home according to ASHRAE standard 90.1. The 2700 square foot home uses around 350 therms and 4500 kWh with its two occupants. My superinsulation retrofit cost around $45 per square foot including kitchen, bathroom, and basement remodeling.
The Best Strategy
The superinsulation retrofit strategy is to air-seal and insulate the existing structure from outdoors. This strategy allows the residents to remain and avoids having to demolish the interior finish and to treat the difficult and discontinuous surfaces from indoors.
My strategy on my last retrofit included these steps.
- Suck the existing insulation out of the attic,
- Air-seal the attic with spray foam
- Re-insulate the attic to R-50
- Remove the exterior siding
- Replace the existing windows with triple-pane windows with foam-insulated sashes and frames (U=0.17)
- Cover the exterior walls from above the top plate to 4 feet below grade with 2.5-inch high-density polystyrene board (R-12)
- Replace the 2-inch fiberglass in the 2by4 walls with R-15 unfaced batts by removing the drywall
- Install half-inch polyisocyanurate foam board on the inside of the exterior-wall studs; install airtight electrical boxes, tape foam-insulation seams and re-drywall
- Covering the exterior basement concrete walls with 2.5-inch high-density polystyrene board and drywalling
- Covering the floor with an inch of high-density polystyrene board (R-4.7) and covering that with 3/4-inch T&G OSB
Controlling the labor for trimming around windows is one of the key components. Our Duxton windows have a 3.5-inch exterior jamb extension that is a real labor saver. It allows you to run the foam over the window’s rough framing to prevent thermal bridging. I installed a foam triangle where the interior wall meets the ceiling and drywalled over that to reduce the typical thermal bridging there.
For more information on reducing home energy use to a minimum, read: The Homeowners Handbook to Energy Efficiency.
Awesome you’ve done that! Joe L did it too his daughter’s house. I’m jealous!
I’ve been wanting to do this for years. My major impediment has been design – how to specify detail for control layers.
I think that problem may be solved: http://www.buildingscience.com/documents/reports/rr-1204-external-insulation-masonry-walls-wood-framed-walls/view
Next is figuring out if anyone in the construction field around here can follow written instructions…