Builders install a variety of products on the exterior of foundations, above-grade walls, and roofs as water-resistive barriers (WRBs), required by the International Residential Code (IRC). Water-resistive barriers are also called weather-resistant barriers, but the former term is now considered preferable. WRBs are buildings’ last and primary exterior water barrier.
WRBs vary widely in their vapor permeability from vapor permeable (more than 10 perms) to vapor impermeable (less than 0.1 perms). WRBs often serve as the home’s designated air barrier. Sometimes the home’s WRB serves as the wall’s designated vapor barrier, below grade or when insulation is installed outside the structural sheathing in cold climates.
Vapor Permeable WRB House Wraps
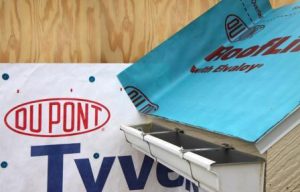
A polyolefin WRB attached with plastic cap nails and a vapor permeable roof membrane protect this new home from water penetration.
Polyolifin films, including polyethylene and polypropylene are the most common WRBs used over exterior frame walls. Their primary purpose is to repel leaked rain water and prevent the water from penetrating the wood sheathing. These plastic-film WRBs are manufactured with microscopic openings that stop air and liquid water while allowing water vapor to pass through. The openings are through tiny holes poked in the material (perforated) or exist between the fibers of a fibrous paper (non-perforated). Experts seem to prefer the non-perforated variety because of better water resistance. Many homes employ their vapor-permeable WRBs as air barriers but these lightweight WRBs are seldom good air barriers because of poor detailing and damage during construction.
One problem with permeable polyolifin WRBs is that builders use staples that create holes that leak water. Instead you should use plastic-cap nails to fasten the WRB to the sheathing.
Another problem with permeable polyolifin films is that ultraviolet (UV) sunlight, wind, and frost damage them. These weather forces can reduce the film’s durability and render the film unable to function as designed. Some WRB products are UV resistant and may remain durable up to 3 months exposed to the weather, but don’t count on it.
Back-primed siding, cedar siding, stucco, soap, sealants and other chemicals can interact chemically with some WRBs. Verify that the WRB you select is compatible with the other building materials that you’ll install near them.
Polyethylene Vapor-Barrier WRB
Some designers and builders are adopting the strategy of installing an air-vapor barrier on the exterior wood sheathing of the wood-frame wall. In this strategy, the workers install most or all of the insulation to the outside of this air/vapor barrier.
Polyethylene film (6 mil) is still the most common exterior air/vapor barrier. However, weather damages polyethylene film the same way weather damages the vapor-permeable films.
Fully Adhered Membranes
Fully adhered WRB membrane are used for WRBs on above-grade walls, foundation walls, and roofs. They provide superior and durable performance as water-proofing and vapor barrier for masonry foundation walls. Othe types of membranes are very open to the passage of water vapor.
Builders occasionally use these membranes as air-vapor-barrier WRBs above grade. Their superior performance depends on the combination of full adhesion and the flexibility to bridge gaps that may expand or contract with temperature variation, water-vapor adsorbsion, or settling.
These fully adhered membranes are a rubberized asphalt bonded to polyethylene, aluminum foil, or both. This type of WRB has a film-protected adhesive side that adheres to primed wood or concrete. The liquid primer is specific to the proprietary WRB membrane. Always use the primer, transitional membrane, and other materials that are specified by the manufacturer to install a complete membrane system.
Liquid-Applied WRB Membranes
The rubberized WRB is also available as a liquid for the same purpose as the flexible WRB sheeting. These proprietary products may include a filler mastic, a thick flashing coat, and a thinner main primary coating.
The liquid-applied membranes may offer the best quality as well as a reasonable installation time. The material itself is considerably more expensive than house wrap.
Always prepare your substrate according to the manufacturer’s instructions. Realize that splinters and rough surfaces aren’t compatible with a liquid-applied membrane. Follow the manufacturer’s instructions faithfully. Use all the materials that are specified by the manufacturer to install a complete liquid-applied membrane system.
Liquid-Applied Waterproofing and Damp-Proofing
The IRC requires waterproofing for foundation walls that border dirt on one side and living space on the other. Workers spray, paint, or trowel waterproofing onto a clean concrete surface to resist water and water-vapor intrusion. Waterproofing is usually 40 mils or more thick.
Builders commonly use less expensive damp-proofing for crawl space foundations. A light sprayed damp-proofing membrane (3 mils or less) is somewhat vapor permeable depending on its thickness. Painted or troweled-on damp-proofing (10 mils or less) is less vapor permeable than sprayed-on.